What Type of Construction Are Most Commercial Buildings?
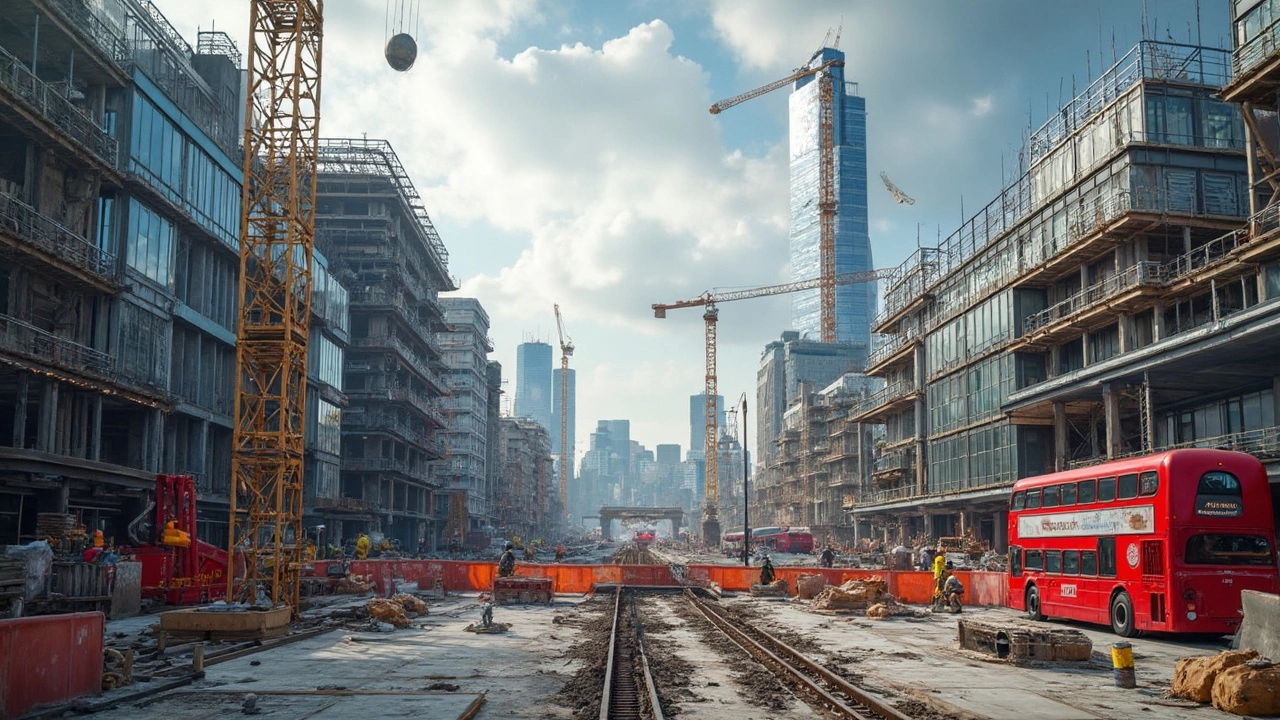
Ever walked past an office tower or a strip mall and wondered what holds that thing up? Commercial buildings don’t just spring up from the ground—they stick with a handful of proven construction types for good reasons. If you take a peek behind all the glass, metal, and polished concrete, you'll find that steel frame and reinforced concrete are the real backbone of most commercial construction out there.
Why do these construction methods stick around year after year? It’s all about strength, speed, and flexibility. Developers want buildings that can take a beating, go up fast, and maybe even change shape inside when tenants swap out. Steel and concrete just make life easier, from the architect’s sketch right up to move-in day. If you’re thinking of building or investing, knowing what’s actually inside the walls can help you spot deals, avoid headaches, and maybe even impress your contractor friends.
- Common Construction Methods
- Materials That Dominate the Market
- Why Steel Framing Leads the Pack
- Emerging Trends in Commercial Construction
- Smart Tips for Building Owners and Investors
Common Construction Methods
Walk into pretty much any city, and you’ll see commercial buildings that look different on the outside but have a lot in common on the inside. It’s no accident. Builders stick to a few construction methods that work well for offices, warehouses, shopping centers, and restaurants. Here’s what usually shows up on the blueprint.
- Steel frame construction: By far the most common for commercial properties. Steel beams support everything, letting architects go as tall and wide as needed without worrying about wood warping or termite trouble. It also means you can have those huge open spaces you see in lobbies or big box stores.
- Concrete frame (reinforced): Here, big concrete columns and beams form the main structure. It’s strong, fireproof, and often used for parking garages, hospitals, and medium-rise office buildings.
- Pre-engineered metal buildings: If you need fast construction, metal buildings go up quicker than just about anything else. Think warehouses, auto shops, and even some schools.
- Masonry construction: Brick or concrete block walls used to carry a lot of the load, especially in mid-20th-century buildings. You still see this method in retail strips and smaller offices.
- Wood frame: Almost never used for large commercial spaces, but you’ll find it in low-rise offices, restaurants, or motels, especially in areas with low seismic risk and cheaper land.
Steel frame and reinforced concrete dominate because they’re reliable, they work for everything from four floors to forty, and they meet strict safety codes. It’s not just about brute strength—these methods also speed up the build and keep insurance rates lower.
To get specific, check out this snapshot from recent industry stats:
Construction Method | Typical Use | Share of New Commercial Buildings (U.S., 2023) |
---|---|---|
Steel Frame | Office Towers, Retail, Hotels | 49% |
Reinforced Concrete | Parking, Hospitals, Midsize Offices | 33% |
Pre-engineered Metal | Warehouses, Gyms, Light Industrial | 13% |
Masonry | Strip Malls, Small Offices | 4% |
Wood Frame | Small Offices, Motels, Restaurants | 1% |
If you’re scouting sites or planning a build, knowing what’s standard can help with budgeting, picking contractors, or even just understanding why that insurance quote is what it is.
Materials That Dominate the Market
Walk onto any commercial construction site and you’ll probably spot the same core materials again and again: steel, concrete, glass, and sometimes masonry. The reason these materials stay at the top isn’t just because everyone’s in a rut—each one offers a specific advantage that matches the fast pace and big demands of modern buildings.
The real MVP has to be steel. Think skyscrapers, big box stores, or warehouses—the bones of those buildings usually come from steel frames. Steel is strong, flexible, and lighter than traditional brick or stone. It helps builders create open spaces with fewer columns, which means bigger, more usable floor areas.
Concrete’s not far behind. You’ll find it in foundations, floors, walls, and sometimes even the exterior. Concrete shines in fire resistance and soundproofing. It can be poured into almost any shape, making it a go-to for custom facades and details.
Glass has boomed since people started loving brighter, more energy-efficient offices. It’s not just for looks—today’s commercial buildings often feature curtain walls made almost entirely of glass, fitted over steel or concrete frames. This combo lets in tons of natural light while still supporting the structure.
- Commercial construction often pairs these materials together—think steel skeletons with concrete floors and glass walls. It’s the blend that gives modern office parks, shopping centers, and hotels that clean, high-tech vibe.
- Masonry (think bricks and concrete blocks) pops up in low-rise buildings and some historic remodels. It’s good for insulation and durability but not as common as steel and concrete in new large-scale projects.
Here’s a quick look at how common these materials are in U.S. commercial builds, based on data from the National Institute of Building Sciences:
Material | Estimated Market Share (%) |
---|---|
Steel (frame) | ~50 |
Concrete (flatwork & structure) | ~35 |
Glass (curtain walls/windows) | ~10 |
Masonry | ~5 |
If you’re planning a project, think about the local climate, cost, building rules, and how much space you need. Sometimes mixing materials—or picking one over another—can save cash or speed up construction. The “right” material isn’t just about tradition; it’s about making a smart call for your location and goals.
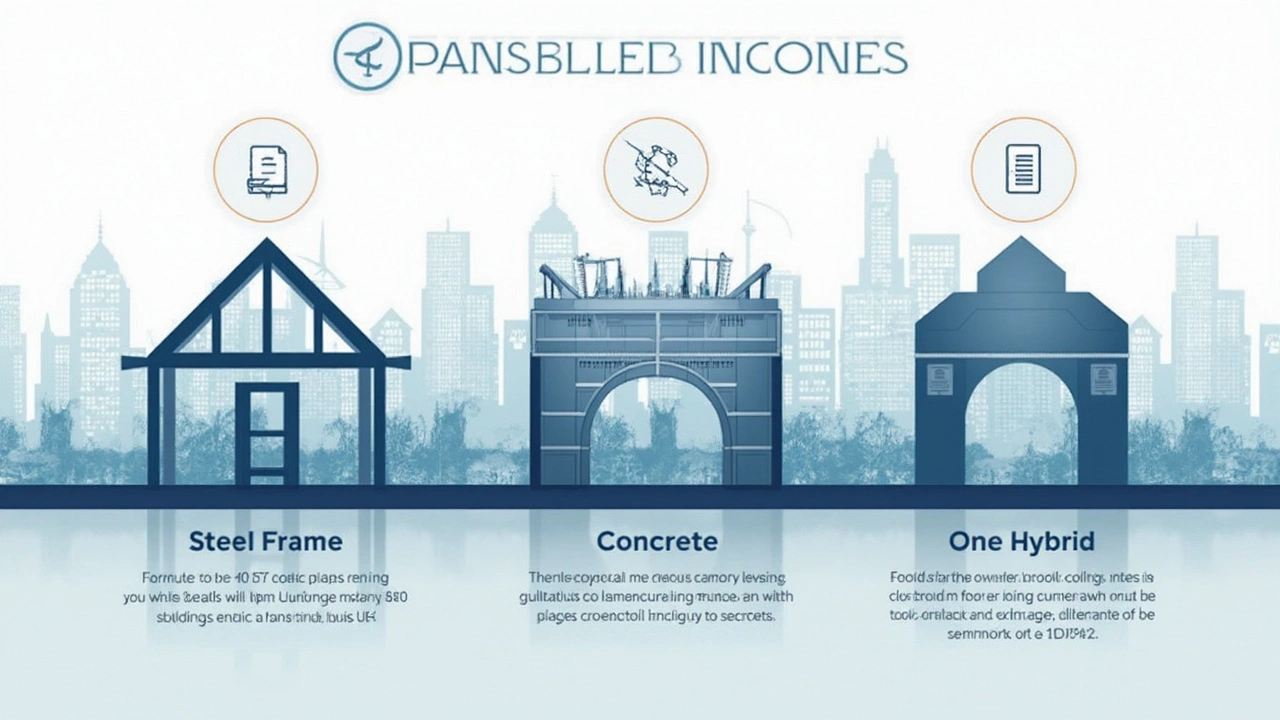
Why Steel Framing Leads the Pack
If you look at modern skylines, it’s no accident that so many tall buildings stick with steel. Commercial construction sides with steel framing for a bunch of practical reasons: strength, speed, cost, and flexibility win out every time. Steel framing makes designing open floor plans way easier because you don’t need thick, heavy walls everywhere for support. That’s why you see it in everything from hospitals to shopping centers.
Steel isn’t just tough—it handles earthquakes, wind, and fire better than wood. That makes insurance folks happy and keeps tenants safer. Even more, it’s quick to put up. Contractors can work year-round since the pieces come pre-made and just snap together on-site, like a giant set of building blocks.
- Most commercial buildings above three stories use steel frames—think of high-rise offices, hotels, and stadiums.
- Steel can span big open spaces without needing columns everywhere, perfect for showrooms and open-plan offices.
- It’s recyclable too, and almost 90% of structural steel used in new projects is recycled material, which is good for companies chasing LEED certification.
Here’s how steel framing stacks up against other common construction types:
Construction Type | Avg. Construction Speed | Seismic/Flood Resistance | Avg. Lifespan (years) |
---|---|---|---|
Steel Frame | 6-12 months | High | 50+ |
Reinforced Concrete | 9-18 months | High | 60+ |
Wood Frame | 4-8 months | Low (above 3 stories) | 30-50 |
One more perk? If you ever need to change up the layout or expand, steel frames are much easier (and cheaper) to adapt than concrete or wood. Plus, fewer columns mean more room for people, equipment, or inventory. So, if you’re thinking big—literally or financially—steel framing often makes the most sense.
Emerging Trends in Commercial Construction
Commercial construction is no stranger to change—especially when costs, sustainability, and tech are on everyone’s mind. Right now, the industry’s moving faster than ever. We’re seeing new approaches that save money, boost efficiency, and keep the planet in mind. You’ll spot these upgrades even in your local shopping center or office park.
For starters, green building is everywhere. Certifications like LEED (Leadership in Energy and Environmental Design) are now way more than just a nice-to-have. More building owners are asking for solar panels, high-performance insulation, and advanced HVAC systems that use way less energy. As of last year, nearly 40% of new commercial projects aimed for green certifications—ten years ago that number was less than 20%.
Modular construction is gaining real traction, too. Instead of building everything on-site, crews assemble sections in factories and piece them together like giant Legos. This cuts construction time by at least 20%, and less mess on the ground means fewer delays. For hotels or basic office spaces, this is huge—the quicker it's built, the faster it earns money.
Tech is shaking things up as well. Drones check job sites from the sky in minutes. 3D modeling helps teams spot mistakes before the first shovel hits dirt. Some companies use robots to lay bricks or even print concrete walls. This isn’t sci-fi—it’s happening right now and making construction smoother.
Here’s a snapshot of how some of these trends stack up in the industry:
Trend | 2021 Adoption Rate (%) | 2025 Projected Adoption Rate (%) |
---|---|---|
LEED/Green Building | 38 | 52 |
Modular Construction | 12 | 26 |
Digital Project Management | 44 | 61 |
3D Printing Elements | 5 | 14 |
One thing’s clear: commercial construction is getting a major upgrade thanks to strong demand for greener, smarter, and more flexible buildings. If you’re planning to build or invest, paying attention to these trends can give you an edge—whether that means lower energy bills, shorter project timelines, or just better spaces that attract more tenants.
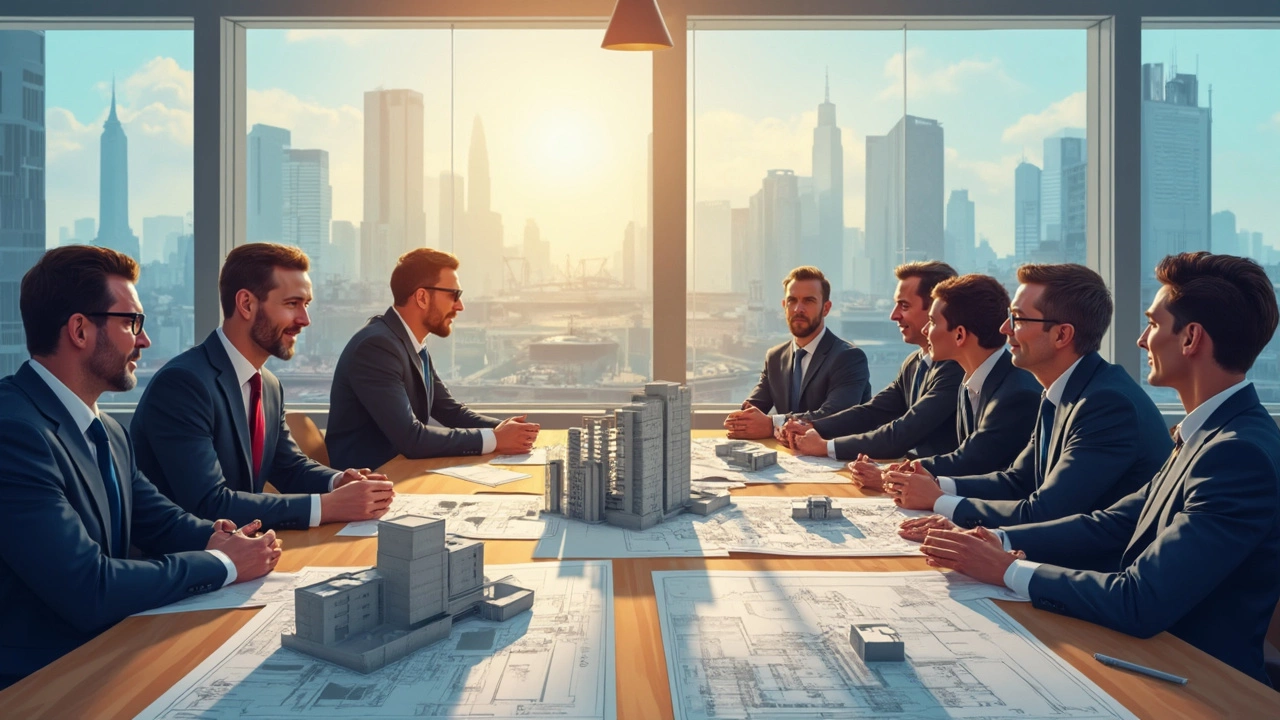
Smart Tips for Building Owners and Investors
If you own a building or want to invest in commercial construction, you want returns, not regrets. Here’s what really matters once the paperwork’s signed and your money’s in the game.
- Check the building’s bones. Steel frames and reinforced concrete last, but both need regular checkups. Schedule structural inspections at least every three years—small cracks or rust can quickly become expensive problems if ignored.
- Stay ahead with energy upgrades. The U.S. Department of Energy says commercial buildings that invest in high-efficiency systems can cut energy costs by around 30%. Look at upgrading to LED lighting, smart thermostats, or even solar panels if state incentives are solid in your area.
- Flexibility pays off. Modern tenants want spaces they can customize. Buildings with open floor plans and fewer load-bearing walls lease up faster and re-tenant with less hassle. Think about modular walls or movable partitions—they’re worth the up-front investment.
- Fire safety means savings. Properties with steel or concrete construction can earn lower insurance premiums because they’re less likely to burn. Double-check your fire suppression and alarm systems—they not only save lives, but also help your bottom line.
- Always know local codes. The 2024 commercial International Building Code (IBC) added stricter rules on ventilation and accessibility. Staying out of legal trouble protects your assets and makes sure your property attracts big-name tenants who care about compliance.
To give you a quick sense of how much building type affects costs, here’s a real-world comparison of annual maintenance averages:
Building Type | Average Yearly Maintenance Cost/sq ft | Expected Lifespan |
---|---|---|
Steel Frame | $1.50 | 50+ years |
Reinforced Concrete | $1.40 | 60+ years |
Wood Frame | $2.20 | 30-40 years |
If you want to boost returns, keep your eye on these numbers and don’t just look at the pretty renderings. Solid construction and smart upgrades deliver value you can see, year after year.