Understanding the 1 3 Rule in Commercial Construction
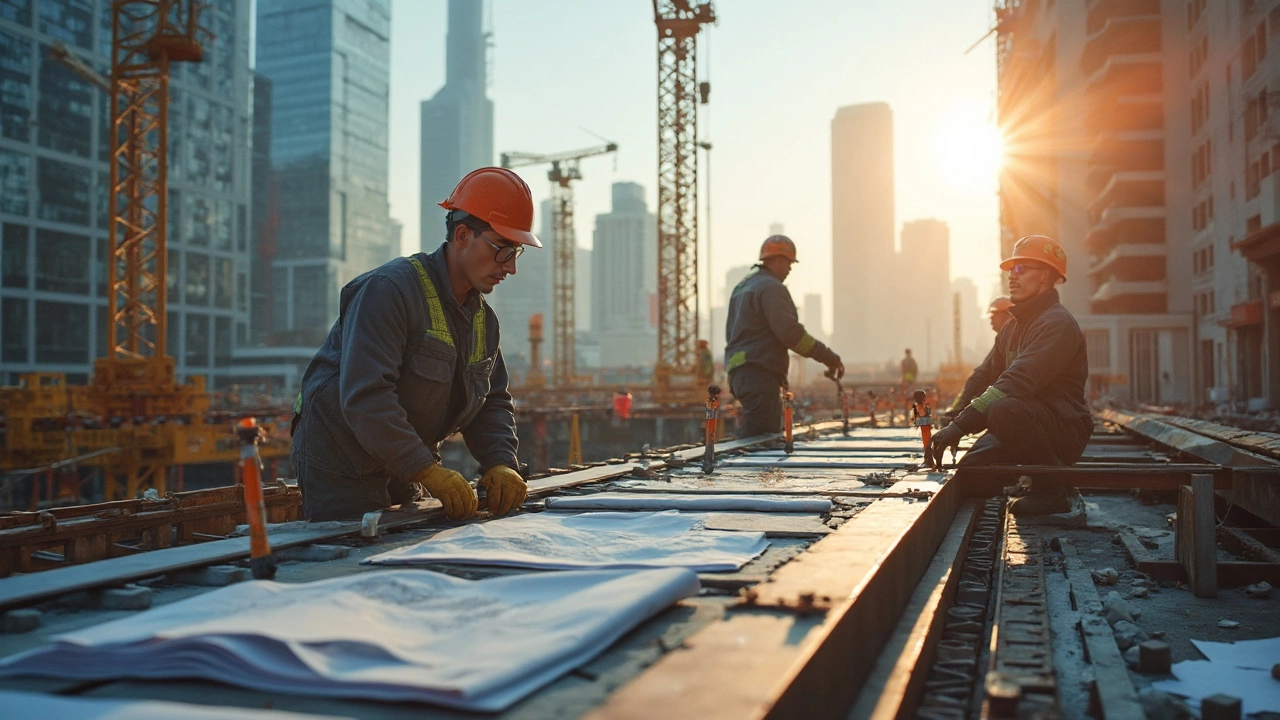
Ever wondered why some buildings stand the test of time while others crumble? The 1 3 Rule might be one of those unsung heroes in construction. This simple guideline dictates that the thickness of a structural component, typically a wall, should be at least one-third of its height. Sounds easy, right? But there's more to it than meets the eye.
This rule isn't just a formula tossed around in construction meetings. It plays a critical role in preventing structural instability, particularly in commercial buildings. Ignoring it can lead to some pretty costly blunders. Think about the towering high-rises and industrial hubs that populate our cities. They need to remain safe and sturdy, and that's where the 1 3 Rule kicks in.
So, why should you care? Well, if you're involved in commercial construction, understanding and applying this rule can make or break your project. Doing it right not only ensures safety but also keeps you in line with regulations, avoiding those expensive penalties. Stick around as we unravel how this rule works in real life, sharing some extra tips to keep you in the clear.
- The Basics of the 1 3 Rule
- Why the 1 3 Rule Matters
- Real-World Applications
- Tips for Compliance
- Avoiding Common Mistakes
The Basics of the 1 3 Rule
The 1 3 rule is a fundamental principle that governs the structural integrity in commercial construction. At its core, this rule mandates that for any standing structure, particularly walls, the thickness should be at least one-third of its total height. This ensures that the structure has the necessary stability to withstand various forces it might encounter.
This is not just an arbitrary guideline. It's based on sound engineering principles and decades of observation. By maintaining this ratio, you allow for adequate load-bearing capacity while minimizing material usage without compromising on safety. This rule becomes a critical talking point during the design phase of any commercial construction project since it impacts both cost and safety.
The Science Behind It
Why one-third? It comes down to center of gravity and balance. A structure that is adequately wide relative to its height can better distribute forces, such as wind or seismic activity. As a result, it prevents tipping or collapsing.
Let's break this down with a simple illustration. Imagine building a stack of blocks. If your tower is excessively tall but very narrow, it becomes susceptible to the slightest push. Adding more blocks at the base (increasing thickness) provides much-needed support.
Practical Application
In practical terms, applying the 1 3 rule is fairly straightforward. When drafting building plans, architects and engineers will incorporate this ratio into their designs. It becomes a quick and straightforward checkpoint to ensure compliance without needing detailed calculations early on.
However, the rule is more flexible in real-world applications. While it serves as an excellent guideline for most scenarios, certain materials and construction methods might allow for deviations. The key is knowing when and where these exceptions apply.
Real-World Example
Consider a commercial office building project. If the planned walls are supposed to be 15 feet high, this rule suggests the thickness should not be less than 5 feet. While this might seem excessive for some materials, for others, it's ideal, especially when considering local weather conditions or seismic activities.
It's these kinds of informed decisions that often separate the pros from the novices in the construction game. Experts can apply the rule intelligently, adapting to specific needs without compromising safety or budget.
Why the 1 3 Rule Matters
The 1 3 Rule isn’t just some arbitrary guideline in the construction world; it’s a critical principle that ensures the safety and durability of a building. This rule helps maintain the structural integrity of walls, especially in commercial construction, where the stakes are high. A misstep here can lead to walls bowing out or, even worse, collapsing.
Let's think about those multistory commercial buildings. Their structural components are under a lot of stress. Following the 1 3 Rule means if a wall is, say, 30 feet high, it should be at least 10 feet thick. This proportion prevents it from buckling under its own weight or from external forces like wind and earthquakes.
Regulatory Compliance
The 1 3 Rule aligns with building codes in many regions, serving as a benchmark for structural safety. Abiding by such standards isn't just good practice; it's often a legal requirement. Forgetting this rule could land you in hot water with building inspectors, leading to costly delays and fines.
Cost Efficiency
You might think thicker walls mean more materials and higher costs, but it’s a trade-off that pays off. What’s the point of a cheaper build if it leads to repairs or, heaven forbid, accidents down the line? Investing in the right proportions minimizes long-term costs and hassles.
Historical Precedents
If we look back, many of our architectural wonders stand tall today because they adhered to principles much like the 1 3 Rule. Ancient Roman and Greek structures, though built without modern engineering, often followed similar guidelines, emphasizing the importance of balance and stability.
So, when kicking off a commercial construction project, ensuring your walls meet the 1 3 requirement is crucial. It safeguards not just your investment but also the people who walk within those walls every day.
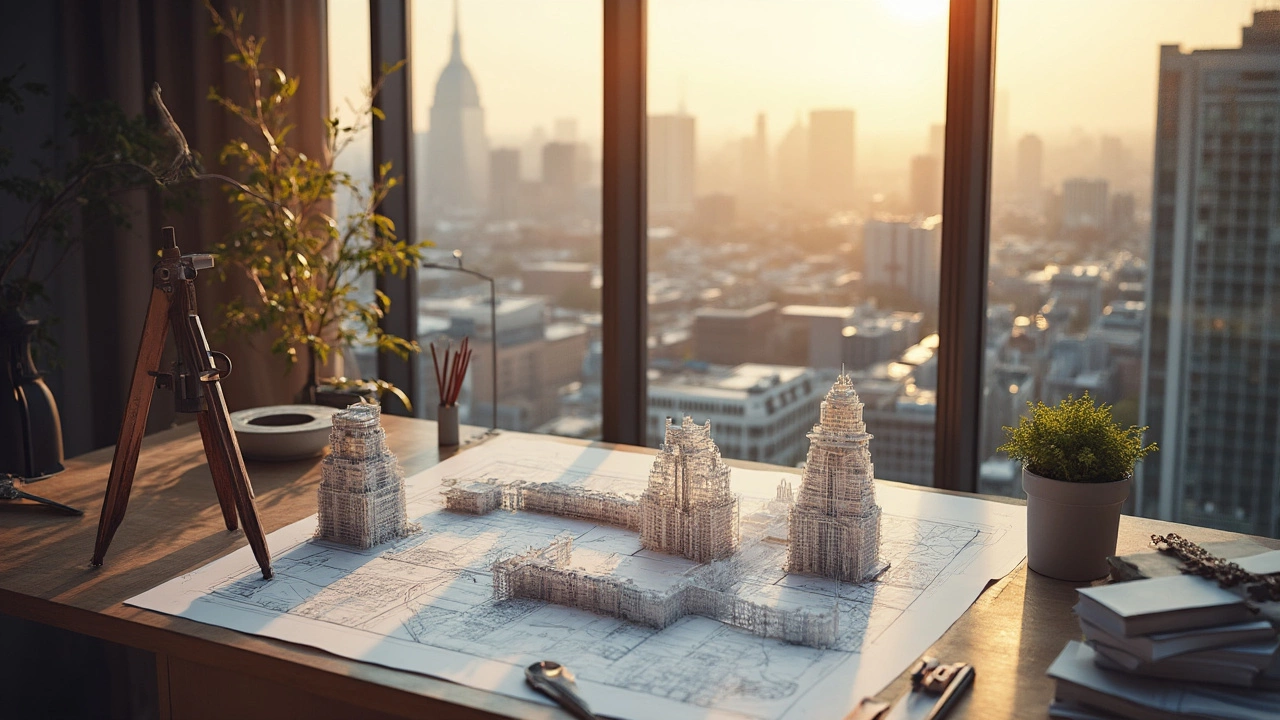
Real-World Applications
Alright, so how does the 1 3 rule really come into play outside of textbooks? If you look around at any commercial construction site, whether it's a new mall or a sprawling office complex, the 1 3 Rule is silently working to ensure structural integrity.
Take high-rise buildings, for example. These towering giants, often found at the heart of any business district, need to handle not just the loads from floors above but also the elements like wind and rain. The rule helps in designing walls that are thick enough to support these stresses while optimizing material costs. No one wants a skyscraper swaying more than it should!
In the world of commercial construction, warehouses also benefit hugely from the 1 3 Rule. Consider a warehouse filled with heavy goods; the walls must not only support the roof but also resist lateral pressures from wind or even internal stresses like vibrations from heavy machinery. That's where the magic 'one-third' thickness really makes a difference.
Modern Residential Projects
It's not just the big players that benefit. Modern residential projects, especially multi-story apartments and condos, also rely on this rule. Using it ensures that these structures remain both durable and aesthetically pleasing, keeping residents safe and sound.
Choosing the Right Materials
Now, let’s talk materials. Depending on what you're working with—be it concrete, steel, or wood—the application of the 1 3 Rule might differ slightly. The key is making sure that your wall materials can handle both the one-third thickness requirement and the necessary load. For example, steel might allow for a thinner wall compared to traditional concrete because of its strength.
Structure Type | Typical Wall Material | Wall Thickness Ratio |
---|---|---|
High-Rise Building | Steel | 1/3 to 1/4 the height |
Warehouse | Concrete | 1/3 the height |
Residential Condo | Mixed Materials | 1/3 the height |
When applied correctly, the 1 3 rule not only protects the building but boosts confidence in investors and stakeholders, reassuring them of solid, safe investments. So if you're working on a project or investing in one, keep an eye out for this rule. It’s more than just numbers—it’s about standing strong for the long haul!
Tips for Compliance
Navigating the construction world can be tricky, especially with all those rules flying around. But sticking to the 1 3 rule doesn't have to be a headache. Here, I’m sharing some practical tips to make sure you're on the right track.
Know Your Measurements Inside Out
Before laying those bricks, double-check your measurements. The 1 3 rule requires the thickness of a wall to be at least a third of its height. Simple math, but getting it wrong can lead to structural instability.
Use Quality Materials
Materials play a huge role in how well this rule works. You can't skimp on quality here. Quality bricks and concrete make a world of difference in meeting the 1 3 rule requirements.
Consult the Experts
Working with a seasoned engineer or architect? Good call! These pros can ensure you're sticking to the rule without missing those tiny details. They know how to make structures both safe and cost-effective.
“In the fast-paced world of construction, adhering to established rules like the 1 3 guideline not only ensures safety but enhances longevity,” - John Miller, Senior Structural Engineer.
Stay Updated on Regulations
Regulations can change, so keep an eye out for any updates in commercial construction. Local regulations might have specific requirements beyond the 1 3 rule, adding another layer of complexity.
Regular Inspections
After building, don’t skip the inspections. Routine checks help catch any potential compliance issues early before they're a bigger problem.
Steps | Description |
---|---|
1 | Get the correct measurements |
2 | Choose top-quality materials |
3 | Engage with experts for guidance |
4 | Keep track of regulation changes |
5 | Conduct routine inspections |
By focusing on these tips, you’ll ensure compliance and help keep everything running smoothly on site. Remember, ignoring something as fundamental as the 1 3 rule isn't worth the risks. Keeping a sharp focus on details will save you time and money in the long run.
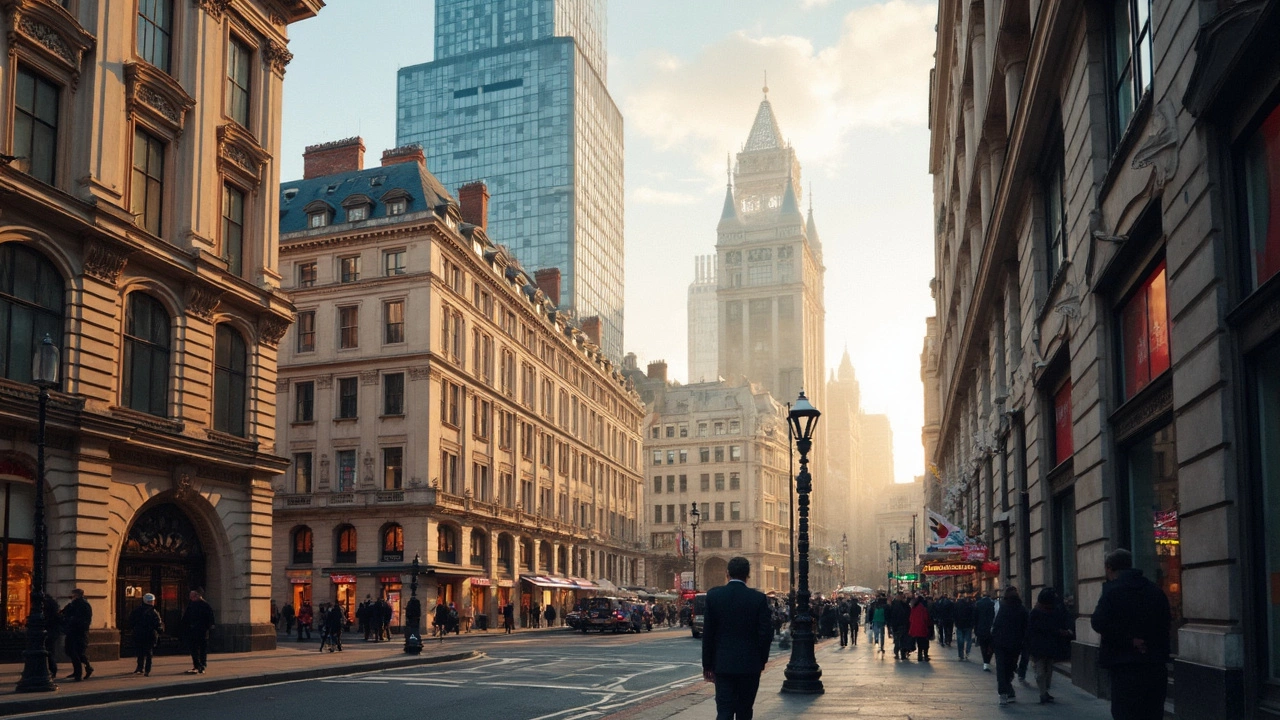
Avoiding Common Mistakes
In the world of commercial construction, even a small oversight can lead to big problems. So, how do you make sure you’re following the 1 3 Rule correctly? Let's look at some common pitfalls and how to avoid them.
Misjudging Measurements
First up, misjudging the height-to-thickness ratio can lead to unsafe structures. Always double-check your measurements. Double checking is not just a suggestion; it's a must. A lot of professionals recommend having a second pair of eyes to verify calculations.
Ignoring Load Factors
Another common mistake? Overlooking load factors. The 1 3 Rule doesn't operate in a vacuum. You gotta consider additional loads the structure will bear like equipment, furniture, and even human weight. Make sure to consult with an engineer to address these factors.
Skipping Regulations
Skipping out on building codes and guidelines is a big no-no. They're there for a reason. A project that's not compliant can run into endless red tape and legal issues, straining your budget and timeline.
Communication Gaps
Miscommunication can be disastrous. Everyone involved from architects to contractors should be on the same page about the specifications of the 1 3 Rule. Regular meetings help keep everyone aligned, reducing risks of error.
Overlooking Environmental Impact
At times, people overlook the environment's effect on structures that comply with the 1 3 Rule. Weather conditions and natural disasters can influence the safety and durability of structures. Always factor in these external risks.
Remember, it's always better to catch mistakes in the planning phase rather than deal with costly fixes down the line. Follow these practical steps, engage the right people, and you'll keep your construction project on a safe and compliant path.