Cheapest Building Method: How to Save Big on New Builds

Dreaming of a brand new place that doesn’t eat up your life savings? You’re not alone. Most people want to know the cheapest way to build, but there are a ton of myths out there. Spoiler: it’s not always about picking the tiniest house or doing it all yourself with no help. Costs add up fast for stuff you never see coming—like land prep, permits, or even hauling in materials from far away.
If you’re hoping to build for less, it pays—literally—to know exactly what things really cost and why. It’s not just about what you build on, but how you build, the materials you pick, and how handy you actually are (or willing to become). Did you know using shipping containers or straw bales is gaining steam as a cheap way to toss up tough, quirky homes? Or that many builders save thousands just by going with ready-made modular parts instead of classic brick and block?
- The Real Cost Drivers
- Cheap Materials That Work
- Modular, Prefab, and Alternative Builds
- DIY vs. Contractor—What Really Saves Money?
- Permits, Inspections, and Legal Shortcuts
- Smart Tips for Slashing Costs
The Real Cost Drivers
If you’re out to find the cheapest building method, you have to break down where your money actually goes. People are often blown away to see that the cost of the land is usually just the beginning. Labor, materials, and regulations can easily be bigger bites out of your budget than anything you do on site.
Here’s what really eats into your home-building budget—and what you can do about it:
- Labor Costs: Labor often soaks up almost half the total spend, especially in places with high wages. Skilled trades like electricians and plumbers never come cheap. If you have sweat equity (willingness and ability to do some dirty work yourself), you can chip away at this expense.
- Materials: Lumber, concrete, insulation, roofing—every item has a price tag, and recent years have sent some material costs sky-high. Sourcing materials locally, using recycled parts, or picking simple designs can drop these figures down.
- Permits and Fees: Most towns won’t let you break ground without permits. These can add up big time—think $5,000-$20,000 in some cities just for approvals and inspections.
- Site Prep: If your land needs clearing, leveling, or utility hookups, costs balloon fast. It’s cheaper to build where utilities already exist and the soil is stable.
- Design and Size: The bigger and fancier you go, the more expensive. Just shaving a couple hundred square feet off your plan could save you tens of thousands.
Check out some typical percentages to see what usually drives costs in a new build:
Expense | Estimated % of Budget |
---|---|
Labor | 35% - 50% |
Materials | 30% - 45% |
Permits/Fees | 5% - 15% |
Site Prep | 5% - 10% |
Design/Engineering | 2% - 5% |
The lesson? If slashing your price tag is the main goal, keep it simple. Location, design, and what you’re willing to tackle yourself matter way more than fancy blueprints or trendy tech. Sometimes just moving out of a strict building zone or going smaller cuts years off a mortgage.
Cheap Materials That Work
When you’re trying to build on a budget, your material choices make or break your project. Some people think you have to sacrifice quality, but plenty of affordable construction options are tough, safe, and look good too. Stick-framing with standard timber is still a staple for a reason—lumber is affordable, easy to find, and most builders know how to work with it. But there are even cheaper options if you’re willing to think outside the box.
Concrete blocks are a classic for low-cost homes, especially for foundations and walls. They hold up to bad weather, bugs, and fire. Saving on materials is also about what you use the most of—so if you swap traditional bricks for concrete blocks or poured concrete, your wallet will thank you. Another shockingly cheap route? Insulated concrete forms (ICFs). They cost a bit more up front but cut down on future energy bills because of their great insulation.
Going even cheaper, some people are turning to materials like:
- Shipping containers: If you’re cool with an industrial vibe, a basic weathered container shell can start around $2,500. You’ll need to cut in doors and windows, but these things are basically solid metal boxes—crazy strong and quick to set up.
- Straw bales: Sounds odd, but stacking straw inside a simple frame gives amazing insulation. Finish it right, and no one’s the wiser.
- Structural Insulated Panels (SIPs): They go up fast and are super energy-efficient, saving you money long-term.
Don't forget simple finishes. Hardboard siding, metal roofing, and unfinished plywood for inside walls drastically drop your costs compared to brick, tile, and plaster. Go for polished concrete floors instead of hardwood—no sanding, no big bills, and almost zero upkeep.
Material | Approximate Cost per sq ft (2024, US) | Main Benefit |
---|---|---|
Framing Lumber | $1.50–$3.00 | Widely available, easy build |
Concrete Block | $1.20–$1.60 | Strong, weather-resistant |
Shipping Container | $2.00–$3.00 | Fast setup, solid structure |
SIPs | $5.00–$7.00 | Quick install, energy savings |
Straw Bale | $1.00–$2.00 | Cheap, super insulation |
If you really want a cheapest building method, hunt for surplus or recycled stuff: used doors, windows, leftover tiles, and even reclaimed bricks from demolition. Some folks have cut up to 30% of their build costs by scouring local auctions, salvage yards, or just networking in building groups. Every piece you get for free, or next to it, is cash that stays in your pocket.
Modular, Prefab, and Alternative Builds
If you’re looking for the cheapest building method that won’t leave you with a money pit, modular and prefab homes are hard to beat. These houses are built in factories, then shipped out and put together on-site. They go up fast—sometimes in just a couple of weeks after delivery—and since so much is done off-site, you don’t pay as much for labor or surprise delays.
Prefab isn’t just about boxy cabins or slick modern cubes. Companies now offer a crazy variety, from pretty traditional looks to wild, off-grid setups. Here’s what makes them cheap compared to classic new builds:
- Bulk buying materials at the factory keeps prices down.
- Assembly line building means less wasted materials and faster work.
- Weather delays and costly on-site mix-ups are way less common.
Then there’s the world of alternative builds, which goes beyond factory houses:
- Shipping container homes—People have made super sturdy, energy-efficient houses out of used containers. They’re strong, easy to stack, and a fraction of the cost of pouring a full concrete frame.
- Earthbag and straw bale homes—For those who don’t mind getting their hands dirty, stacking straw bales or earthbags creates thick, insulated walls at a fraction of the cost of bricks. They’re also super eco-friendly.
- Tiny homes on trailers—These portable homes can sneak around permits and sometimes skip foundation costs entirely. A basic DIY tiny house build can run as little as $25,000, compared to the six-figure cost of a regular new build.
Here’s a quick look at estimated costs for different new builds that use modular or alternative methods:
Method | Estimated Cost per sq. ft. (USD) |
---|---|
Modular Home | $90 – $150 |
Prefab Panel Home | $80 – $130 |
Shipping Container Home | $100 – $170 |
Straw Bale Home | $60 – $110 |
Tiny Home (DIY) | $45 – $90 |
Just keep in mind, hookup costs (water, sewer, power) and local codes still apply. Some towns make it harder to use non-traditional builds, so it pays to look up your local rules before you fall for a budget dream.
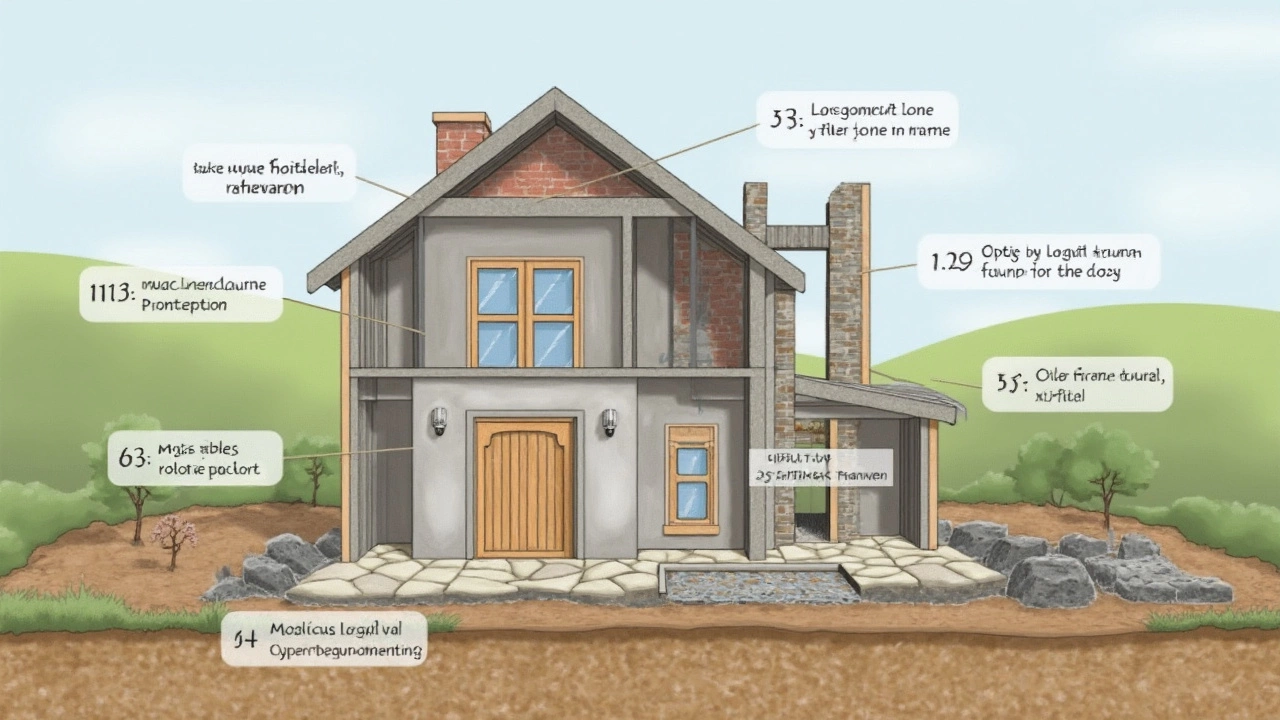
DIY vs. Contractor—What Really Saves Money?
This question keeps a lot of folks up at night. Is it cheaper if you roll up your sleeves and tackle your new builds yourself? Or is it smart to just hire a pro and avoid all the headaches? The answer depends on what you actually know and what you’re willing to learn—and how much risk you can handle if things go sideways.
Going the DIY route can seriously cut labor costs. In most builds, labor is 30-40% of the total price. If you can handle jobs like painting, tiling, or even framing, you could chop thousands off your final bill. But here’s the big catch: mistakes cost money too. If you have to redo work or hire someone to fix a mess, your savings can vanish fast. Plus, jobs like wiring, plumbing, and structural work aren’t just tough—they have legal codes and safety rules. Goofing them up can get expensive, especially if inspectors get involved.
Contractors, on the other hand, don’t come cheap, but they bring speed and know-how. They usually finish faster and—they’ve got teams and the right tools. Pros also get materials at trade prices, which can save you cash if you trust them to pass along the deals. On the flip side, hiring a contractor adds markups and overhead.
- Cheapest building method fans tend to do some kind of mix: DIY the simple stuff, hire pros for the tricky bits.
- Project management is a hidden money trap. If you’re managing subs and ordering materials, that’s a part-time job—hope you can handle the stress.
- Insurance matters. DIYers sometimes forget you need coverage in case someone gets hurt, even if it’s just a friend helping out. Contractors include this in their fee.
Check out this sample cost breakdown for a 1,500 sq ft affordable construction project if you do it yourself versus hiring contractors for everything:
Task | DIY Cost | Contractor Cost |
---|---|---|
Framing | $13,000 | $22,000 |
Drywall | $3,000 | $6,000 |
Painting | $1,000 | $4,000 |
Flooring (Laminate) | $2,500 | $6,500 |
Total | $19,500 | $38,500 |
Yeah, you could almost cut your costs in half. But that requires skills, patience, time, and a lot of hustle. If you’re not confident, a good middle ground is hiring a contractor for the big, code-required stuff (like the foundation and wiring) and doing the finishing work yourself.
Bottom line: If you want the cheapest building method for your new build, DIY what you can—but don’t be afraid to call in a pro when it counts. Saving money won’t mean much if you’re living in a half-finished house or fixing unseen DIY disasters for years to come.
Permits, Inspections, and Legal Shortcuts
If you skip permits or fudge inspections, you might save cash up front, but you’re asking for headaches—or a massive fine—down the road. Every city and county has rules, and even the cheapest building method has to pass minimum standards. That means you can’t just start pouring concrete and hope no one notices.
You’ll need a building permit for almost any new construction, even simple sheds in some parts of the US. Getting caught building without one? You could get a stop-work order, legal fees, or a forced tear-down. Inspections are there so no one gets hurt, and so your home won’t fall apart in a few years.
Here’s where you can actually save:
- Dig around your local city or county website for a clear fee schedule. In some spots, rural areas have lower permit costs or fewer required inspections than the city.
- Look out for self-certification for small projects—some towns let qualified builders or even homeowners sign off on basic steps instead of paying an outside inspector every time.
- If you’re using affordable construction methods like modular panels or prefab kits, a lot of the heavy lifting (paperwork-wise) is already handled by the company, so you pay less in review fees.
People get tripped up with surprise expenses. For example, some areas make you get extra permits for things like septic tanks, driveways, or even fences. Here’s a real breakdown for typical permit costs in the US (as of late 2024):
Type | Avg. Cost (USD) |
---|---|
Basic Building Permit | $1,000 - $3,500 |
Electrical Permit | $50 - $500 |
Plumbing Permit | $50 - $550 |
Septic Permit | $400 - $2,000 |
Don’t be tempted by guys offering to “get you around” permits for cash. If an appraiser or future buyer finds out your work isn’t legal, you’ll lose way more money in the end. Instead, talk to the building department early. They’ll tell you what you really need, what you can skip, and sometimes even grant exceptions if you’re building in a totally rural spot.
Bottom line: Using the cheapest building method means playing by the rules. You’ll keep your project legal, safe, and way easier to sell or refinance someday.
Smart Tips for Slashing Costs
Getting a cheapest building method isn’t about skipping quality—it’s all about working smart, not just harder. Cutting corners the right way can make or break your budget.
- Stick to a simple shape. Think plain rectangles or basic cubes for your home design. Every bay window, dormer, or curve ramps up both materials and labor costs. Research shows single-story rectangles are up to 30% cheaper to build than houses with complex layouts or lots of corners.
- Use local materials. Hauling stuff from out of town drains your wallet. Look up what’s common and cheap where you live. For example, in some parts of the Midwest, concrete block goes for about 20% less than elsewhere. Sourcing wood, stone, or even straw bales nearby can add up to big savings.
- Buy materials in bulk. Big-box stores and supply shops usually cut deals if you ask. In 2024, a study from Builder magazine found buying bulk framing lumber dropped costs by 12-15% for most DIY home builds. Team up with a neighbor if you only need a smaller order.
- Go small and plan for upgrades later. Build a tight, efficient footprint—then add a deck, extra room, or basement later if you need it. Starting with less square footage means less immediate spending, especially with today’s wild lumber prices.
- Reuse and recycle whenever you can. Salvaged windows, doors, and fixtures from old demo sites can save hundreds—sometimes even more. A lot of builders check local "buy nothing" groups or visit the Habitat for Humanity ReStore for deals.
- Do the easy jobs yourself. No need to pay someone to paint or install basic trim if you’ve got a steady hand. Homeowners who pitched in on finishes in their new builds saved, on average, $8,000–$10,000, according to a 2023 HomeAdvisor survey.
- Compare quotes—and negotiate. Don’t take the first number a contractor gives you. Always get at least three quotes. Last year, homeowners who negotiated estimates shaved 7-10% off final expenses.
Cost-Saving Move | Average Savings |
---|---|
Simple rectangular single-story shape | 20-30% of build cost |
Buying materials in bulk | 12-15% |
DIY painting/trimming | $8,000–$10,000 |
Local/salvaged materials | Varies, up to 25% |
If you remember nothing else, remember this: The cheapest building method always means sweating every detail in planning. Don’t rush it—every clever trick, bulk-buy, or bit of DIY lets you stretch your cash a whole lot further.