Essential Raw Materials for Modern Construction: Complete Guide
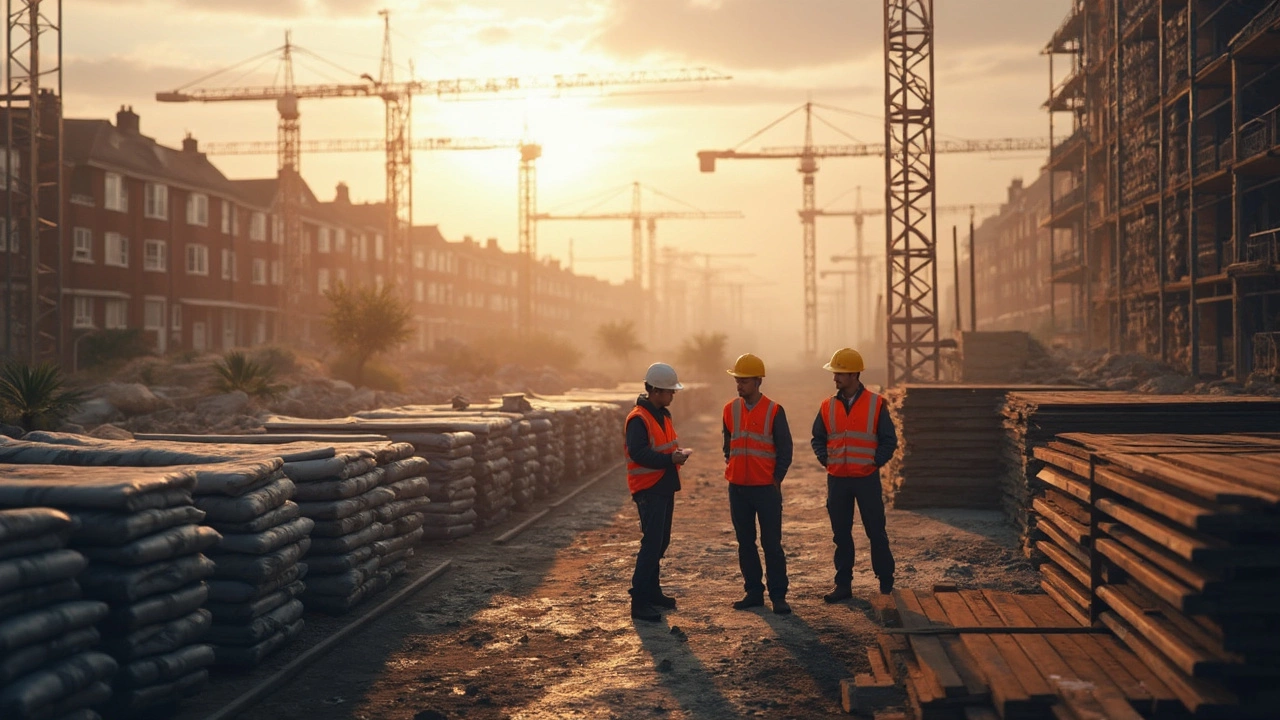
Ever wonder what goes into building the places we live, work, and relax? Behind every wall, under every floor, and inside every skyline is a mix of raw materials that make it all possible. Concrete jungles aren’t just a metaphor when you realize how much sand and gravel goes into a single office tower. From clay bricks in century-old Auckland villas to ultra-strong steel girders in new highrises, the real story hides right under our feet. But what actually goes into a construction project today? Let’s sort through the gritty details and untangle which raw materials really matter in our modern world.
Concrete: The Backbone of Modern Buildings
If there’s one material that literally holds cities together, it’s concrete. This tough mix starts simple—just cement, sand, gravel, and water—but when you get the formula right, you end up with something incredibly strong. Ordinary Portland Cement (OPC) is the star of the show; you’ll see it in almost every new building project from Auckland to Boston. Here’s a fun fact: about four tonnes of concrete are produced per person worldwide every year. That’s more than a thousand kilograms per person, each year, to build roads, bridges, foundations, and towers.
Getting the perfect blend takes skill. Add too much water, the concrete loses its strength; not enough, and it’s impossible to work with. There are also additives like fly ash or silica fume—byproducts from industrial processes—that improve strength, make the cure time quicker, or help concrete stand up to harsh weather. It's not just about the mix, either. Gravel size, sand texture, and the purity of the water all count. Poor-quality sand or dirty water can weaken everything and lead to damage over time.
One thing many people forget is concrete’s environmental cost. It’s a major source of global carbon dioxide emissions. A lot of innovation now focuses on lowering its carbon footprint—whether by using recycled aggregate, lower-carbon cements, or even capturing CO2 and blending it directly into new mixes. In New Zealand, there’s a big push to use locally sourced materials, cutting down shipping and supporting sustainability. Recycled rubble from demolished buildings sometimes ends up directly in new mixes, saving precious resources.
Table: Common Concrete Additives and Their Functions
Additive | Purpose | Typical Dosage |
---|---|---|
Fly Ash | Increases strength, reduces cost | 15–30% by weight |
Silica Fume | Improves durability and chemical resistance | 5–10% by weight |
Plasticizers | Improves workability without extra water | 0.1–0.5% by weight |
Quick tip: When ordering concrete for a project, always confirm if it needs to be high-strength (for structural columns) or standard (for outdoor steps or garden walls). This little detail saves a lot of headaches down the line.
Steel and Metals: Strength, Flexibility, and Endless Possibilities
If concrete is the backbone, then steel is the muscle that lets buildings reach for the sky. Steel shows up everywhere—beams and columns in skyscrapers, mesh inside concrete slabs, even the brackets that hold up your deck. New Zealand mostly imports its structural steel, but processing happens right here, and recycled metals are on the rise. The beauty of steel is how much it can handle. Try this on for size: One tonne of structural steel can support the same load as a small army of timber beams—plus it lasts, it bends without breaking, and you can recycle it endlessly.
When it comes to picking which steel goes into the mix, builders look at grades. Fe500, for example, is common in big commercial projects because it’s strong but not brittle. Stainless steel sees use in places that fight off moisture, like kitchens and coastal builds. Galvanized steel—with its protective zinc coat—laughs in the face of rain and time. Alongside steel, you get copper in wiring and pipes, aluminium in window frames and roofing, and even specialty metals like titanium in some architect-designed features.
Of course, steel production isn’t exactly gentle on the planet. Mining iron ore, firing up furnaces, and hauling raw metal all add up. On the upside, the metal recycling loop is strong: Over 80% of steel for construction in NZ comes from recycled sources. That means your new garage may well have a bit of old car chassis or iron fence in its bones.
Quick tip: When buying metal for construction, check for certifications (like NZS 3404 or ISO 9001) and always ask about recycled content. It’s better for the environment and can save costs if you play the market right.
Another bit that deserves mention—metals don’t work alone. They form the skeleton that supports spans of concrete, glass walls, and even green roofs. Some new apartment builds mix steel frame towers with solid timber floors, merging speed with sustainability. Hybrid structures aren’t just trendy—they’re practical and help cut both build time and carbon emissions.
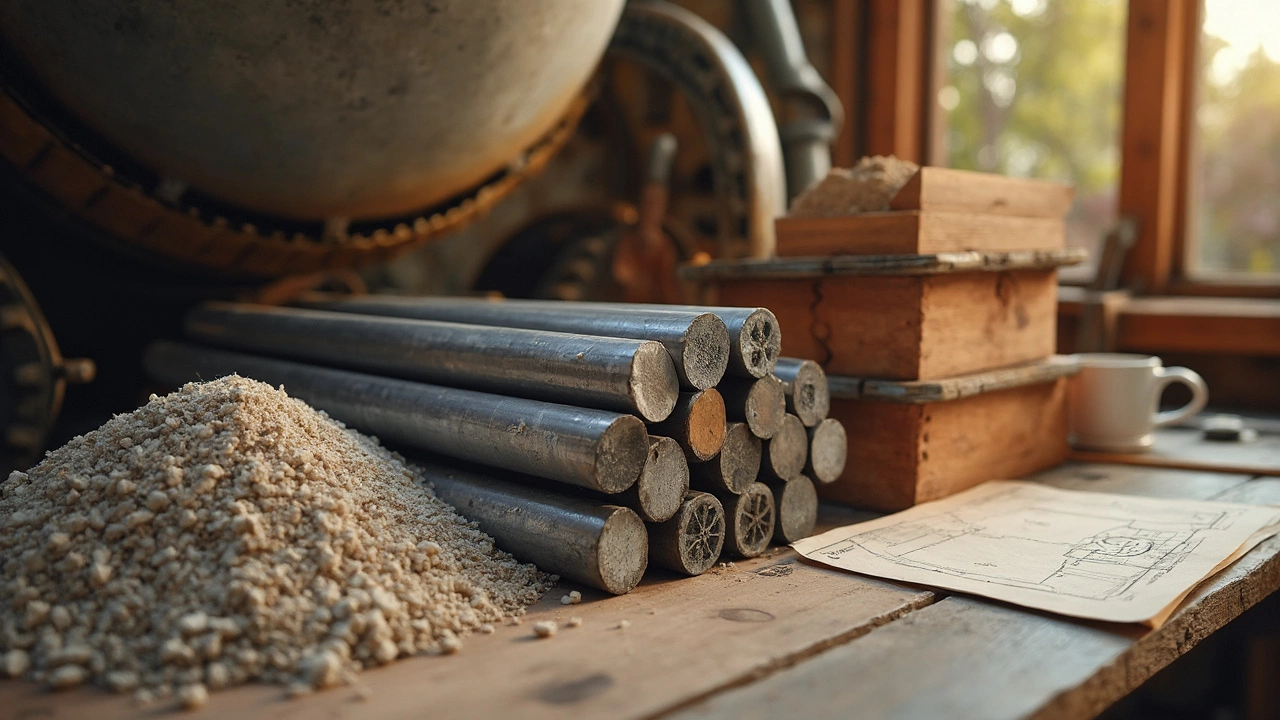
Timber, Stone, and Bricks: Earth’s Oldest Construction Allies
Way before steel and concrete, wood, stone, and fired clay held buildings together. Even now, these materials haven’t lost their touch. Timber is the most renewable resource in the bunch, especially here in New Zealand, where pine, rimu, and beech forests cover huge areas. Engineered wood like laminated veneer lumber (LVL) and cross-laminated timber (CLT) are taking center stage in modern mid-rise buildings. They harness timber’s natural strength in a package that’s precise, fire-resistant, and nearly as tough as steel.
But why use one material when you can blend? A classic Auckland villa might have a stone foundation, brick exterior walls, and timber floors. Each has its secret superpower—stone stands up to earthquakes better than you’d think, while bricks absorb and release heat, keeping homes cooler in summer and warmer in winter. Timber is a dream for renovations; you can cut, nail, glue, or screw it with regular tools and swap out damaged bits without tearing down walls.
Of course, not all timber is equal. Using treated pine prevents bugs, moisture, and decay, while unprotected woods are better for interiors. Stone can be local—greywacke or basalt in Auckland—or imported when architects want a specific look. Brick quality depends on the clay source and firing temperature. A poorly fired brick crumbles, a well-fired one will last a century or more.
Here’s a tip: For renovation projects, try to match both the size and color of new bricks or timber to what’s already there. Little mismatches stand out fast. Also, keep in mind that old bricks often outlast new ones; repurposing saves waste and adds genuine character.
Check out this table with renown properties:
Material | Main Use | Durability (Years) |
---|---|---|
Radiata Pine (NZ) | Framing, trusses, CLT panels | 30-60 |
Brick | Walls, paths, facades | 75-150 |
Stone (Basalt, Greywacke) | Foundations, walls | 100+ |
Choosing the right mix depends on your build needs, climate risks, and, honestly, budget. Natural materials offer a warmth and texture that concrete or steel alone can’t match. They’re also easier to reuse, repurpose, and—maybe best of all—age with real style.
Glass, Plastics, and New-Gen Building Materials
It’s not all rock and rebar in today’s construction. Modern architects lean on glass walls, high-performance plastics, and composites that break old rules. Glass used to mean fragile windows and tiny panes, but now, toughened or laminated glass panels can span entire building faces while blocking heat and noise. Some new glass even cleans itself using sunlight, making skyscraper maintenance a little less daunting.
Plastics pop up in more spots than you’d guess. PVC pipes run through the walls and underground; polycarbonate sheets let in light but shrug off hail; compact foams insulate roofs and floors. Then there’s composite decking, which fuses sawdust and recycled plastic into boards that look like wood but last twice as long. These new-gen materials are lighter, less prone to damage, and often save cash on long jobs.
Here’s where it gets really interesting. Hybrid building materials—like fibre-reinforced concrete, insulated panels, and even carbon fibre beams—are changing what’s possible. Fibre concrete takes regular old cement and toughens it up with glass or synthetic strands, stopping cracks before they start. Structural insulated panels (SIPs) sandwich thick insulation between wood or metal skins, making walls that lock in heat and stand up to storms.
Tip: If you’re serious about energy bills, look for high-R-value insulation, low-E glass, and sealed plastic barriers. The upfront cost pays off in comfort and savings down the road. And don’t forget, some of the best innovations are invisible. Vapour barriers, waterproof membranes, high-tech adhesives—all of it helps keep structures safe and solid, year after year.
So, what’s the future? It’s a mix of the tried-and-true and the brand new. Building smarter, not just bigger, with an eye on sustainability, resilience, and, most of all, practical results right now—not just down the track. Whether you’re laying a backyard deck or planning the next icon on Auckland’s skyline, starting with the right construction raw materials lays the groundwork for lasting success.